
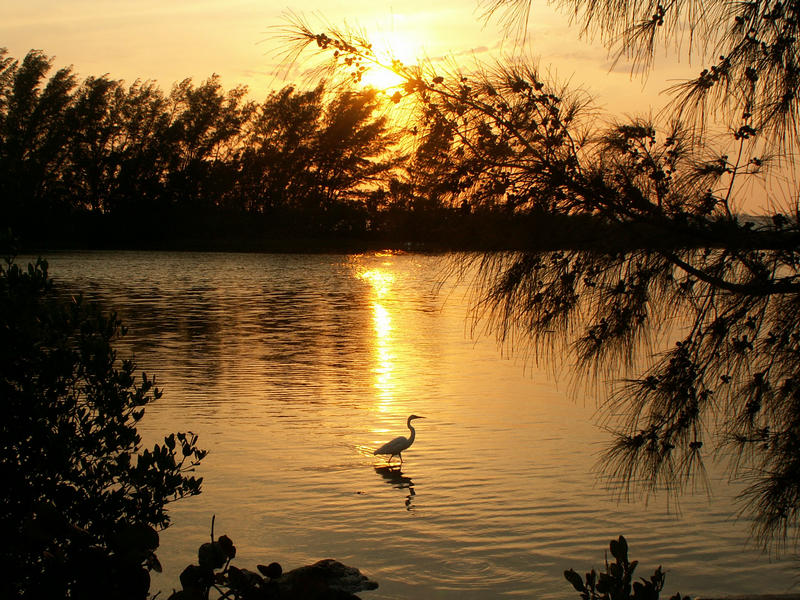
SOP Site Manager Remediation Guide
- Home
- Divisions
- Division of Waste Management
- Petroleum Restoration Program
- SOP Site Manager Remediation Guide
Petroleum-Restoration Quick links
- Petroleum Restoration Program
- PRP Contacts
- Announcements & Upcoming Events
- Administrative Guidance
- Agency Term Contracts (ATC)
- Assessment Guidance
- Competitive Procurement System
- Database Reports & Site Files
- General Technical Guidance
- Innovative Technology Acceptance Program
- Monthly Dashboard Update
- Petroleum Cleanup Programs
- Presentations & Brochures
- Priority Score Funding Threshold History
- Procedures & Guidance Documents
- Qualified Contractor Information
- Related Links
- Remediation Guidance
- Rules and Statutes
- SOP
- Templates, Forms, Tools and Guidance
- Webpage Updates History
- Weekly Encumbrance Approval
- All Petroleum-Restoration content
Active Remediation
Overview
The active remediation phase starts after the site assessment approval order has been issued. Active remediation for the Petroleum Restoration Program is governed by Chapter 62-780, Florida Administrative Code (F.A.C.), and other rules, laws and documents referenced therein. Specifically, Chapter 62-780.700, F.A.C. Active Remediation, although requirements listed in other sections of the rule may also apply.
The goal when addressing a petroleum discharge either through source removal, active remediation or natural attenuation monitoring is to reach closure and the issuance of a Site Rehabilitation Completion Order (SRCO). The risk management options level I, II and III (RMO I, II and III) found in Chapter 62-780.680, F.A.C., are authorized in section 376.30701(5), F.S., Site Selection and Cleanup Criteria, and were developed to provide equivalent levels of protection to human health and the environment. If a Conditional Closure Agreement was executed for the site, review the interim restrictive covenant and work with ATC so that remedial actions are designed to achieve the conditional closure endpoint. Whenever possible the selection of a closure option should be established prior to the implementation of a Remedial Action Plan (RAP) and upon consultation with the property owner and/or responsible party. Site mangers should be familiar with the criteria for No Further Action and No Further Action with Controls as specified in Ch. 62-780.680, F.A.C.
Risk Evaluation and Conceptual Site Model (CSM)
Closure strategies for a site must be based on an understanding of site conditions. The Conceptual Site Model (CSM) is a tool used to assist in making site management decisions. Site conditions and assessment data can be compiled into a CSM. The CSM should evolve as site conditions become better defined and as remedial progress occurs. The CSM is composed of the following components:
- Description of the source of contamination.
- The extent of contamination of the soil and groundwater (plume depth and horizontal extents).
- The characteristics of the physical/geologic/chemical/environmental setting below grade and on the ground surface.
- A description of risk to humans and the environment posed by exposure to the contamination.
- A description of the current and potential exposure pathways to the contamination.
- An evaluation of remedial strategies suited for the site.
Pilot Testing and Remedial Action Planning
The first scope of work in the active remediation phase will be for pilot testing (if necessary) and remedial action planning. Remedial Action Plans (RAPs) must be prepared in accordance with DEP guidance and Chapter 62-780.700, F.A.C. Specific guidance for RAPs can be found on the PRP Remediation Guidance webpage. The ATC includes two levels of RAPs and four levels of limited scope RAPs or RAP Modification along with detailed descriptions of what level of RAP is appropriate. A Pre-RAP meeting is typically scheduled before a RAP is prepared to discuss the CSM and remediation goals including proposed technology, need for a pilot test, and the level of RAP required.
The first task in the scope will be for Pay Item 1-2 a. No cost HASP. The second task may consist of supplemental site assessment (SSA) needed for preparation of the RAP or a pilot test plan. Pilot testing is usually not performed if there is a nearby site that has similar CSM, particularly lithology and contaminant conditions, and has had successful remediation results. Data from the nearby site may be used in lieu of performing a new pilot test for remedial action planning. If a pilot test is deemed necessary it can be added via change order based on the specifications in the approved pilot test plan. The last two tasks will be for the completed RAP and Construction Drawings and other applicable Schedule of Pay Items (SPI).
For more information, please visit the SPI Guidance and PRP Standard Specification Details.
Demolition of Structures
Generally, the demolition of structures is to be avoided as part of site rehabilitation if at all possible. However, on occasion when it is clearly recommended as part of the most cost effective cleanup option, the site manager must refer the site to their Team Leader at FDEP in Tallahassee for evaluation before discussing demolition with the Owner, Tenants or further with a Contractor. The Team Leader will evaluate the recommendation and consult with the Program Administrator and Office of General Counsel. Site managers should not discuss demolition, solicit information on demolition, or provide information on demolition to site owners or contractors until receiving written guidance from the Program Administrator to do so.
Types of Remedial Systems
Air sparging (AS) is the most common technology used to remediate petroleum contamination. AS systems use compressed air directed into treatment wells screened below the water table. The air causes the dissolved petroleum to volatize. The vapors created will collect in the soil above the water table. A vacuum extraction (VE) system is used to remove the vapors from the soil. Typical components of a AS system include an air compressor, a heat exchanger (to reduce temperature of compressed air), filters to remove particulates and potential oil carryover from the compressor, air distribution piping, AS wells, system meters and gauges, and backflow prevention (to prevent water from entering compressor when not running). AS systems may use vertical, angled or horizontal wells.
An underground injection control (UIC) notice is required for sparging wells. This notice can be completed by the contractor or site manager, should be included in the RAP, and is attached to the RAP approval order.
Bio Sparging (BS) systems are low-flow AS systems, generally less than 4 ft3/min. Flow rates are selected to minimize the generation of vapors in favor of providing oxygen to native bacteria in order to promote biological degradation of petroleum contaminants. BS systems have the same components as an AS system. BS may be equipped with a VE system to ensure vapors are controlled.
Vacuum Extraction (VE) systems use blowers or compressors to apply a vacuum to soil above the water table causing air to flow through the soil and vapors to be collected and treated. Typical components of a VE system include a vacuum blower/compressor, an air-water separator, groundwater collection tank/treatment/disposal system, system piping, treatment wells, off-gas treatment, and system meters and gauges.
Multi-Phase/Dual-Phase Extraction (MPX/DPX) systems use high vacuum blowers and/or in-well (submersible) pumps to extract contaminated vapors, groundwater and free product in one stream to the treatment system. These technologies are used at sites with less transmissive lithology and where it is desirable to lower the water table in order to access more vadose soil. Typical components of a MPX/DPX system include a vacuum blower or liquid ring pump, submersible pumps, groundwater collection tank/treatment/disposal system, system piping, treatment wells, and system meters and gauges.
Injection Systems may use chemical oxidation or biological enhancements to reduce contaminant levels. Injectants are delivered below ground using a pump or compressor and treatment points or wells. This technology is highly specialized and most vendors have a proprietary product and/or application method. Typically, these technologies are applied by means of direct push technology.
RAC SOW/SPI
The Site Manager should use the information from the approved RAP, construction drawings and SPI submitted by the contractor to create the remedial action construction (RAC) purchase order. This scope of work will cover treatment point installation, system installation, baseline sampling, startup, and one quarter of operation and maintenance (O&M).
Because of the numerous details being transferred from the RAP to the SPI, careful review should be performed by the site manager and the P.E. The RAC table located in the SOW is designed to collect all these details and help the site manager fill out the SPI. The Trenching Calculations tool and SPI Phase Example Guidance with Mobilization and Per Diem Calculations are also helpful tools for filling out the SPI.
The RAC, O&M and SR Tips to Speed Up PR Processing is also a helpful tool.
Startup Report Review
A system startup report should include data to document that the remediation is in accordance with the approved RAP, Chapter 62-780, F.A.C., and requirements of the purchase order. A checklist of startup items is available in the PRP Remediation Checklist workbook. This report is critical for the remediation stage because it verifies that the remedial activity is performing as designed. The Site Manager should consult with the team P.E. during review in order to ensure that all necessary data has been collected and reported.
Active Remediation Monitoring Reports
All quarterly and annual reports for active remediation monitoring must be in the standard PRP RA Summary Report format and contain all information as required by Chapter 62-780, F.A.C., and DEP guidance. Each annual report must also include an evaluation of cleanup milestones in accordance with the Petroleum Restoration Program Cleanup Milestone Workbook.
The ATC has specific requirements for system runtime. See the Project Managers Guide - Remediation System Runtime Evaluation for guidance for evaluating project runtime.
Source Removal/Excavation
Conventional Source Removal
Conventional excavation involves the use of an excavator or a backhoe. Shoring and or dewatering of the area to be excavated may be required depending on the soil types, depth to water, adjacent buildings or roads, and depth of excavation. Shoring may be done with sheet piling, trench boxes, or LDAs. Clean overburden often can be combined with imported backfill. Also, it is not uncommon to apply biological or chemical enhancements during backfill operations. Proper compaction is critical to avoid subsidence and cracks after the excavation.
Large Diameter Auger (LDA)
LDA rigs historically used to install pilings can also be used to remove contaminated soil. The most common design is overlapping 5-foot diameter holes, although other auger sizes are available. Flowable fill, which is a type of lower strength concrete, is used to fill the borings. Flowable fill can be mixed onsite or be brought in from a batch plant.
Source Removal SOW/SPI
The Site Manager should use the information from the approved RAP, Construction Drawings and SPI submitted by the contractor to create the Source Removal purchase order. This scope of work will cover backfill screening, well abandonment, source removal, and site restoration including well replacement.
Because of the numerous details being transferred from the RAP to the SPI, careful review should be performed by the site manager and the P.E. The Source Removal table located in the SOW is designed to collect all these details and help the site manager fill out the SPI. The SPI Phase Example Guidance with Mobilization and Per Diem Calculations is a helpful tool for filling out the SPI. The RAC, O&M and SR Tips to Speed Up PR Processing is another helpful tool.
Source Removal Report
The source removal report should include data to verify that source removal was performed in accordance with the approved RAP, Chapter 62-780 F.A.C., and purchase order. This report is critical to document that the source removal was performed as planned. The information in this report may include weigh tickets/manifest, disposal volumes and tonnage, backfill compaction results, site restoration documentation, analytical testing results (backfill and confirmatory soil), monitoring well logs dewatering treatment system sampling results, and NPDES reporting. The Site Manager should consult with the team P.G. or P.E. during review in order to ensure that all necessary data has been collected and reported.
Return to: PRP Site Manager Standard Operating Procedures (SOP) webpage.
Return to: SOP Site Manager Guide webpage.
Interested in subscribing to DEP newsletters or receiving DEP updates through email?
Sign UpAbout DEP
The Florida Department of Environmental Protection is the state’s lead agency for environmental management and stewardship – protecting our air, water and land. The vision of the Florida Department of Environmental Protection is to create strong community partnerships, safeguard Florida’s natural resources and enhance its ecosystems.
Learn MoreContact
3900 Commonwealth BoulevardTallahassee, Florida 32399-3000 Public.Services@FloridaDEP.gov 850-245-2118
