
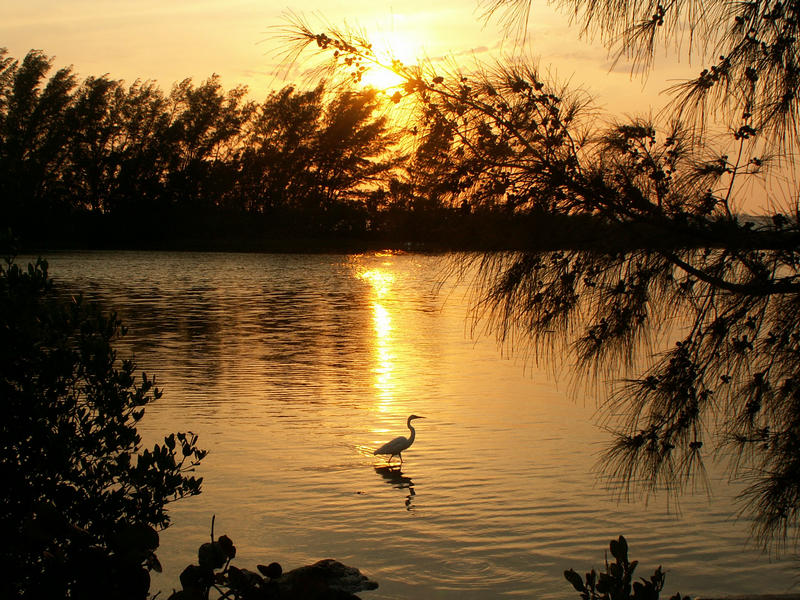
SOP Site Manager Assessment Guide
- Home
- Divisions
- Division of Waste Management
- Petroleum Restoration Program
- SOP Site Manager Assessment Guide
Petroleum-Restoration Quick links
- Petroleum Restoration Program
- PRP Contacts
- Announcements & Upcoming Events
- Administrative Guidance
- Agency Term Contracts (ATC)
- Assessment Guidance
- Competitive Procurement System
- Database Reports & Site Files
- General Technical Guidance
- Innovative Technology Acceptance Program
- Monthly Dashboard Update
- Petroleum Cleanup Programs
- Presentations & Brochures
- Priority Score Funding Threshold History
- Procedures & Guidance Documents
- Qualified Contractor Information
- Related Links
- Remediation Guidance
- Rules and Statutes
- SOP
- Templates, Forms, Tools and Guidance
- Webpage Updates History
- Weekly Encumbrance Approval
- All Petroleum-Restoration content
Overview
Site assessment for the Petroleum Restoration Program is governed by Chapter 62-780, Florida Administrative Code (F.A.C.), and other rules, laws and documents referenced therein. Specifically Chapter 62-780.600, F.A.C. - Site Assessment, although requirements listed in other sections of the rule also may apply.
Note that all field procedures for Petroleum Restoration sites are governed by Chapter 62-160, F.A.C., which has incorporated by reference the Standard Operating Procedures for Field Activities (DEP-SOP-001/01). Please refer directly to the Bureau of Assessment and Restoration Support website for the most current field procedures.
Additional guidance documents and clarification memos are available on the PRP Assessment Guidance webpage.
The Petroleum Restoration Program will fund site assessment work based on the current Priority Score Funding Threshold, with active funding being encumbered for sites with priority scores above the current funding threshold. Site owners or responsible parties may fund site assessment and remediation at their own costs, but must comply with Chapter 62-780, F.A.C., if the work performed is to be reviewed by DEP for site closure. There are three options for securing state funding for site assessment out of priority score, as outlined below:
The end goal of site assessment is to delineate the horizontal and vertical extent of petroleum hydrocarbon impacts in the soil and groundwater as a result of a release of petroleum products. This information is used to evaluate the current exposure and potential risk of exposure to humans and the environment, including multiple pathways of exposure, determine applicable exposure factors and the remedial strategy for the site, and risk management options based on the current and projected land use(s) at the site.
Pre-Assessment
Before assessment begins, or at the earliest point possible during assessment activities, the Site Manager and Agency Term Contractor should begin work on a Conceptual Site Model (CSM). CSM means a written and/or graphic representation of the physical, chemical and biological processes that affect the transport, migration, and actual or potential exposure to contamination in all affected media to human and ecological receptors. The CSM is used to develop and refine the extent of site assessment, support remedial alternative, mitigation and cleanup technology evaluations, and support risk management decisions. The CSM may be prepared or updated at any time during site rehabilitation as new or revised information becomes available. The CSM does not have to be a separate document and is generally a framework to determine what kind of assessment is needed and how to refine the assessment over time.
As the first task in a new assessment scope (with no previous assessment performed, or resuming work on a site that has been parked for several years), the Site Manager and Agency Term Contractor should discuss the site history, current site conditions, and conduct an Assessment Planning Meeting.
The following should be included in Task 1 on new site assessment (no previous assessment, or new ATC on site):
- File Review
- Site Health and Safety Plan
- 1-2.a. No cost HASP for updates on continued work
- 2-1. Site Reconnaissance/Field Measurement Visit
- 20-2. & 20-4. Project Manager & Geologist, 1 hour for Assessment Planning Meeting
- 19-20. Letter Report to summarize Assessment Planning Meeting
The File Review deliverable should include the Historical Site Summary with information based on STCM, Oculus, CLM and the site reconnaissance.
- Storage Tank Contamination Monitoring (STCM)
- OCULUS Document Management System
- Contamination Locator Map (CLM)
Site Reconnaissance
Site reconnaissance should include checking the following:
- Verify site layout compared to site maps if previous assessment has been performed (location of fuel system, building, etc.).
- Verify historic monitoring wells are present and confirm that wells are viable. Consider scoping monitor well gauging pay items.
- Make note of site access for drill rigs. Overhead utilities, swales/drainage ditches, traffic, etc.
- Take numerous photos to document site conditions.
Assessment Planning Meeting
After the site file review and site recon, ATC should set up a telecon/dialogue with the site owner/operator, DEP/LP and drillers to discuss:
- General assessment plan going forward: locations of concern, approximate number of borings/wells, etc.
- Access issues: owner/operator requests, discussion of DTW/lithology/access with drillers to determine appropriate rig to mobilize. Drillers should be able to make suggestions based on their experience.
- Closure Options: conditional closure, LSSI closure if site score is below 30, etc.
- Pre-drilling/Direct Push Technology Scope of Work Site Meeting - Memorandum dated 12/04/17
- Guidance for Implementation of Pre-Drilling/Direct Push Technology Scope of Work Meeting (Updated 5/15/18)
If a Conditional Closure Agreement was executed for the site, review the interim restrictive covenant, discuss endpoints with site owner and work with ATC to assure cleanup approach is designed to achieve the conditional closure goal.
Based on the initial discussion of access, planned work and drill rig use, the ATC should make any changes to the scope of work by Change Order (changing drilling technology, adding contingent work, right-of-way permitting/costs, etc). Involving all parties in initial planning should limit unexpected change orders during assessment.
Standard Operating Procedures PCS-003 - Complete Streamlined Assessment Procedures for Inland Protection Trust Funded Sites provides a framework for designing an assessment plan with minimal delays to completion.
Investigation Locations
When specific information is available about the location of the petroleum discharge through the Discharge Reporting Form, associated reporting or fuel system inspection documents, the Site Manager and Agency Term Contractor should focus initial site investigations on the appropriate locations on the site. Keep in mind that many of the discharges that are being investigated may be up to 30 years old, and subsequent redevelopment may mean that the current fuel system locations do not correspond to where the fuel system was located at the time of the discharge. The initial file review, site reconnaissance, and Assessment Planning Meeting outlined above should confirm current and historic locations of interest at the site.
If no information is available about a specific location for the reported discharge, it can be assumed that the discharge originated with some portion of the fuel storage and dispensing systems. Initial sampling should be performed at the location of fuel storage tanks, fuel dispensers, and documented or suspected location for the fuel lines between the storage tanks and the dispensers.
Investigation near existing active fueling systems can risk a new discharge by damage during site investigation activities. Investigation near overhead or underground utilities can risk damage to the utilities and injury to field staff. Particular care should be taken when working near the active fueling systems and utilities, in accordance with the most current guidance including the Performance Standards for State-Funded Investigations Near Petroleum Storage Systems and Utilities.
Required Laboratory Analytical Sampling
The nature of historical petroleum products stored at the site and the particular discharges that have occurred will determine what laboratory analytical sampling will be required for site assessment. Chapter 62-780, F.A.C. outlines the contaminants of concern for petroleum site assessments.
- Table C – If only Gasoline or Kerosene Analytical Group products were stored at the site.
- Table D – If Used Oil was stored at the site, or if the nature of the petroleum product is not known or not listed in the Gasoline and Kerosene Analytical Groups.
GAG/KAG Discharges
For Gasoline Analytical Group (GAG)/Kerosene Analytical Group (KAG) discharges, samples should be collected for BTEX/MTBE, Polycyclic Aromatic Hydrocarbons (PAH) and Total Recoverable Petroleum Hydrocarbons (TRPH) by the appropriate analytical methods. Initial groundwater samples should also be collected for EDB and Total Lead at one or two wells per source area, or that are suspected of having the highest petroleum concentrations. Supplemental sampling should be limited to the petroleum contaminants that were detected exceeding CTLs in the initial sampling event. Full GAG/KAG groundwater analysis should use the appropriate pay item (9-25) rather than the individual laboratory analysis pay items. See Soil Sampling (GAG/KAG Discharges) Flowchart.
Used Oil or Unknown Discharges
For Used Oil or Unknown discharges, samples should be collected for the Used Oil Group (Priority Pollutant Volatile Organics, Priority Pollutant Extractable Organics, TRPH, Total Arsenic, Total Cadmium, Total Chromium, and Total Lead), by the appropriate analytical methods. Initial groundwater samples should also be collected for Non-Priority Pollutant Organics by the appropriate analytical methods. During the initial sampling, the Used Oil Group sampling should be restricted to one or two samples based on visual staining, highest Organic Vapor Analyzer (OVA) reading if no staining is present, or at the tank/fill port location for the suspected former tank location. Remaining samples can by analyzed for the GAG/KAG Analytical Group. Supplemental sampling should be limited to the petroleum contaminants that were detected exceeding CTLs in the initial sampling event. Used Oil Group analysis should use the appropriate pay items for the group sampling (9-1 and 9-29) rather than the individual laboratory analysis pay items. See Soil Sampling (Used Oil Discharges) Flowchart.
Pretreatment Soil Samples
Laboratory analytical requirements for pretreatment soil sampling varies depending on the petroleum products discharged and the specific disposal facility. The ATC should provide a list of the required laboratory analysis based on the disposal facility and method they are working with. In general, for disposal sites in Florida the typical analyses for KAG/GAG sites can include VOHs, TRPH, Total Arsenic, Total Cadmium, Total Chromium and Total Lead, and typical analyses for Used Oil/Unknown sites can include VOHs, TRPH, Total Arsenic, Total Cadmium, Total Chromium, Total Lead, Total Organic Halogens and PCBs. Some facilities may also require Toxicity Characteristic Leaching Procedure (TCLP) extraction for some of the samples. See Pretreatment Soil Sampling Flowchart.
Soil Assessment
Soil assessment should be performed in accordance with Standard Operating Procedures for Field Activities (DEP-SOP-001/01), particularly FS 3000 Soil Sampling and Standard Operating Procedures PCS-004 - Soil Assessment and Sampling Methods for Florida Bureau of Petroleum Storage Systems Sites. FS 3000 discusses technical procedures for soil sample collection, and PCS-004 discusses variances specific to the Petroleum Restoration Program.
Technologies - When evaluating whether to use hand augers, auger drilling, direct push and/or some other approach for advancing an assessment, a number of factors should be considered; the depth to water, lithology, and estimated extent of contamination are the main factors used to determine the best approach. Consulting with the ATC and drilling subcontractors that have experience with other sites in the area should be considered.
For sites with shallow water tables (i.e., less than 8 feet to 10 feet BLS) where rock is not to be encountered, hand augers should be considered first. (Note: The first 4 feet of a boring need to be hand-extracted anyway so utilizing DPT for shallow water tables is usually impractical.) Hand-augered borings also can be converted to piezometers for collection of groundwater samples for land-based or mobile lab evaluation, and determination of the direction of groundwater flow.
DPT is best suited for screening sites with an intermediate water table (up to 25 feet to 30 feet BLS), complicated lithology, and/or an estimated large plume. At such sites, DPT screening of soil and groundwater will provide a cost-effective method to determine the best locations for shallow and deep monitoring wells.
Auger drilling/split spoons is best suited for screening sites with a deep water table (greater than 30 feet BLS) where rock is not to be encountered, due to the additional power available to the larger rig.
Sonic drilling is best suited for screening sites with a deep water table (greater than 30 feet BLS) or where rock or very tight/stiff lithology or voids are expected to be encountered.
Soil Boring Spacing
During the initial site investigation, soil borings should be advanced in the area indicated as the source of the discharge in site records, or around the area where the fuel system was located during the time of the recorded discharge (the fuel system location may have changed since the discharge was reported). At a minimum, borings should be placed around the outside of the UST area, as near as possible to each dispenser, and along any pipe runs between the tanks and the dispensers. Please observe all safety regulations when advancing borings in the vicinity of the fuel system (See SOP - 17. Utility Clearance). It is also advisable to include a few step-out soil borings during the initial sampling event to begin delineating any OVA exceedances encountered around the fuel system or discharge location.
Generally, soil borings should be spaced at 10-foot to 15-foot intervals when stepping out from confirmed screening or laboratory analytical exceedances, in order to determine sufficient delineation for remediation purposes. Greater spacing can be used during initial assessments to determine the approximate boundaries of soil impacts, especially at larger facilities, with more closely spaced borings placed during supplementary assessment in order to refine the delineation.
During LSA investigations, the purpose of assessment is to determine the presence or absence of petroleum impacts and the approximate size of the plume. Therefore, a larger spacing (approximately 20 feet to 30 feet) can be used when stepping out from the source areas. At smaller sites, it may be appropriate to place step-out soil borings at the site boundaries in order to determine if soil impacts have migrated beyond the site boundaries.
Soil Sampling
Chapter 62-780, F.A.C., mandates the collection of confirmatory soil lab analyses for a minimum of three vadose zone soil samples per source area representing high, medium and low screening results for Gasoline Analytical Group (GAG) and/or Kerosene Analytical Group (KAG) discharges. This data is used to determine if OVA readings correlate with the analytical data, which will allow faster screening and delineation of the soil plume. If there is a correlation, fewer laboratory analytical samples will be required, typically to confirm the plume boundaries. However, if there is no firm correlation between soil screening readings (by OVA/FID or PID), if laboratory analytical results indicate high levels of petroleum hydrocarbon exceeding CTLs, and if active remediation will be performed at the site, it may be beneficial to collect a representative vadose zone soil sample from most or all soil borings advanced, in order to completely delineate vadose zone soil impacts using laboratory data. Soil sampling may also be necessary in the smear zone and/or saturated zone to obtain further data to assist in remedial decisions; please consult with your section engineer to determine if such samples will be beneficial.
During the initial soil investigating, contractors usually will be installing a large number of soil borings to collect OVA data. In order to determine where to collect lab samples, the contractors may be comparing OVA data over several days. In this case, it is allowable to approve additional soil boring pay items (Section 5), in order to return to the locations where the high, medium and low OVA samples will be collected. During supplemental site assessment, where the contractor is stepping out to delineate the soil plume, fewer soil boring locations are required, and the Site Manager and contractor should use the initial assessment data to agree on laboratory sample locations as part of the scope of work. In this case, the contractor will collect the soil samples as instructed, and will not need additional soil boring pay items to collect the laboratory samples. See Scoping Contingent Borings for Soil Sampling guidance.
For the purpose of describing soil sampling strategy in Florida’s petroleum cleanup program, the following definitions for the different soil zones should be used.
- The vadose zone is the area between the land surface and the water table. Since the water table fluctuates, the thickness of the vadose zone varies with the water table. Due to the nature of contamination migration in the soil matrix, soil contamination in the vadose zone is generally restricted to the source area locations.
- The saturated zone is defined as the area below the water table. The top of the saturated zone will vary depending upon the seasons and is sometimes difficult to distinguish from the capillary zone during the drilling event. For this reason, soil borings should be completed to a depth of at least 1 to 2 feet into the water table to ensure that the borings are completed into the saturated zone (unless a variance to this policy has been approved by the PRP).
- The capillary fringe is described as the area directly above the water table where moisture “wicks” upward due to capillary forces, leaving small amounts of water in the pore spaces above the water table. The thickness of the capillary fringe zone is dependent primarily on the type of soils.
- The smear zone is the area of soil contamination that may exist, at varying extents, within the zone of water table fluctuations that have occurred since the time of the petroleum release. Petroleum product floating on top of the water table can become sorbed onto the soils within this zone as the water table fluctuates, potentially leaving a large amount of petroleum product mass that has adhered to the soil grains. This product can remain trapped below the water table as the water table rises. Soil Cleanup Target Levels (soil CTLs) generally apply to the vadose zone (above the water table), but due to water table fluctuations the soil CTLs may or may not apply to the smear zone samples and a case-by-case determination is necessary. It is important to determine whether there is a smear zone and to define the smear zone boundaries as part of a site assessment to allow proper decisions regarding the need for, and scope of, remedial action and the proper placement of the top of well screens (because apparent smear zones, as indicated by elevated OVA readings as the water table is approached, can help estimate historical water table fluctuations at a site).
Laboratory Samples
The selection of sample locations for lab analyses does not need to be based on an exact percentage of the range of field screening results. The objective is to obtain a sample that represents a high screening result, one with a low screening result that is above background, and one with a result as close to the midpoint of screening results as possible. The sample selection should be based on the best judgment of the field personnel in discussion with the ATC geologist and PRP site manager. The goal should be to collect the high from within 10 percent of the highest screening result, the low from within 10 percent of the lowest screening result, and the medium from approximately halfway between these. However, this goal can be adjusted based on the need for the data and the appropriateness of the sampling strategy. In many cases, obtaining a high in the top 25 percent and a low in the bottom 25 percent may be sufficient and more practical.
For subsequent sampling events, the goal of the soil sampling event may be to obtain one or more high, medium or low soil samples that better determine the OVA threshold value indicating the soils are contaminated above the Soil CTLs, or one or more extra high soil samples to assist in making remedial decisions. The high, medium and low soil samples should normally be obtained from separate borings, but on rare occasions (such as when the water table is deep) from different depths in the same boring depending on the nature and extent of the soil contamination. The best strategy is to vary the depths and locations of soil samples as appropriate to obtain data representative of the extent of contamination.
At each GAG or KAG source area, when there are no positive responses above background during soil screening activities, only one soil sample for laboratory analyses should be collected from the suspected source area. If information is not available regarding the depth of the suspected discharge, or if there was a suspected surface spillage (based on the eligibility information), then the sample should be collected from within 2 feet of the ground surface. In the case of aboveground storage tanks, the sample should be collected next to the tank if a containment area is not present, or at the location where the containment area drain valve discharges if a containment area is present. However, if the discharge is suspected to have occurred at depth (such as a ruptured line or fuel tank), then the soil sample should be collected at the depth suspected of having been most impacted. If laboratory analyses indicate that there is petroleum contamination in the soil, then soil assessment should proceed on the assumption that the screening method may not be able to resolve the extent of the soil contamination.
At sites where soil contamination has been confirmed from laboratory results, but it has been demonstrated that soil contamination is not detected by field soil screening devices, then the extent of the soil contamination will need to be defined by laboratory analyzed samples. The sampling locations and the number of samples needed to define the extent of soil contamination exclusively with laboratory analyses should be determined on a site-by-site basis.
SPLP/TRPH Speciation Soil Samples
Synthetic Precipitation Leaching Procedure (SPLP, USEPA Test Method 1312) extractions and analyses of the leachates are performed when there is a question of whether the contamination in the soil at a site will leach to the groundwater at concentrations in excess of groundwater CTLs. The SPLP should be considered only in situations where Direct Exposure soil CTLs are not exceeded but one or more leachability soil CTLs are exceeded. A description of the SPLP testing procedure is outlined in the department’s May 1998 “Guidelines for Assessment and Source Removal of Petroleum Contaminated Soil”.
SPLP tests should not be performed routinely at every site if the leachability- based soil CTLs are exceeded for a soil sample. For example, if the site has a shallow water table and the groundwater is impacted by petroleum hydrocarbons at levels above the groundwater CTLs, then it stands to reason that the contamination in the soil is leaching to the water table (the exception would be when soil contamination sufficient to leach to the groundwater existed in the past, but the soils have since naturally attenuated to a point they are no longer contributing to groundwater contamination). SPLP tests should generally be performed for sites where the groundwater is not impacted at levels above the groundwater CTLs, but the leachability- based soil CTLs are exceeded. Generally it is sufficient to run SPLP extraction and analysis on one or two soil samples with the highest petroleum hydrocarbon concentrations; it is assumed that if those soils will not leach to groundwater, less-impacted soils also will not leach.
When costing in the SPLP analyses in a work order, two separate costs for the SPLP analyses should be included for each SPLP sampling location. The first cost that should be included is for the extraction of the leachate from the soil (EPA Method 1312) and the second cost is for analysis of the leachate by the laboratory (EPA Method 602, 8310, etc., depending on which contaminants were previously detected in the soil above leachability- based soil CTLs). It is important that the laboratory uses a water analysis method capable of achieving the groundwater CTLs for the SPLP leachate test. The results of the SPLP analyses should be compared to the groundwater CTLs and not the leachability- based soil CTLs for each constituent analyzed.
If the default soil CTLs are exceeded for TRPHs, then alternative soil CTLs may be established by performing an additional laboratory analysis that identifies the TRPH class (aromatic or aliphatic), the fractions present for each class, and the concentrations measured for each class. This additional analysis should be performed only if TRPHs are the only contaminant of concern detected above the soil CTLs. Generally it is sufficient to run TRPH Speciation on one or two soil samples with the highest petroleum hydrocarbon concentrations; it is assumed that the ratios of specific TRPH Fractions are the same in all soils associated with the discharge.
If this analysis is to be performed, then two (split) soil samples should be collected from the previous sampling location and depth interval that indicated the TRPH exceedance. One sample should be analyzed using FL-PRO. The second (split) sample should be analyzed for TRPHs using either the Total Petroleum Hydrocarbon Criteria Working Group (TPHCWG) method or the Massachusetts Department of Environmental Protection (MADEP) method. The purpose of collecting split samples is so that the laboratory can first analyze the samples for TRPHs using the FL-PRO method to verify the samples collected are representative of the location of previous TRPH exceedance. Based on the concentration of TRPHs detected during the FL-PRO analysis, a decision can then be made as to whether it is necessary to run the more expensive TPHCWG or MADEP methods.
The concentrations obtained during FL-PRO analyses should be compared to the direct exposure and leachability- based soil CTLs. The concentrations for the TPHCWG method should be compared to each of the TRPH classes and fractions that are listed in Calculated SCTLs for TRPH Fractions (effective April 17, 2005).
Carcinogenic PAHs
Per the May 14, 2007, Quality Assurance and Related Issues memorandum, due to low Groundwater Cleanup Target Level concentrations, if concentrations of benzo(a)anthracene, benzo(b)fluoranthene, dibenz(a,h)anthracene, and indeno(1,2,3-cd)pyrene are not detected, of if one or more are detected but their concentrations do not exceed their respective PQLs, it is considered that the alternative groundwater CTLs are met even if the risk-based groundwater CTLs in Table one of Chapter 62-777, F.A.C., are lower than the PQL. If at least one of the carcinogenic PAHs is detected in the soil sample at a concentration equal to or higher than the Method Detection Limit (MDL), the Total Benzo(a)Pyrene Equivalent concentration should be calculated using the Benzo(a)Pyrene Equivalents Conversion Table for One Sample or Benzo(a)Pyrene Equivalents Conversion Table for Multiple Samples.
Monitoring Well Installation
Soil assessment should be performed in accordance with Standard Operating Procedures for Field Activities (DEP-SOP-001/01), particularly FS 2200 Groundwater Sampling, and Standard Operating Procedures PCS-005 - Groundwater Sampling Standard Operating Procedures Variances and Clarifications for Petroleum Restoration Program Sites and Standard Operating Procedures PCS-006 - Design, Installation, and Placement of Monitoring Wells. FS 2200 discusses technical procedures for groundwater sample collection, and PCS-005 discusses sampling variances specific to the Petroleum Restoration Program.
Technologies
When evaluating whether to use hand augers, auger drilling, direct push and/or some other approach for installing groundwater monitoring wells, a number of factors should be considered; the depth to water, lithology, and estimated extent of contamination are the main factors used to determine the best approach. Consulting with the ATC and drilling subcontractors that have experience with other sites in the area should be considered.
Monitoring wells installed with a conventional drilling rig require a minimum of 2 inches for the annulus located between the well screen and the wall of the borehole; therefore, the minimum borehole diameter for a 2-inch inside diameter (ID) monitoring well installed with a non-direct-push rig is 6 inches. In some circumstances, such as when the aquifer is composed of sand that is similar to the sand pack material, exceptions to the minimum 2-inch annular space for monitoring wells can be made. Variances to the 2-inch annular space requirement must be approved by the PRP prior to the installation of the wells.
Hand augers may be used for sites with shallow water tables (i.e., less than 8 feet to 10 feet BLS) where rock is not to be encountered, if there is no access available for any type of drilling rigs. Hand-augered borings should typically be used only to install temporary monitoring wells or piezometers for collection of groundwater samples for land-based or mobile lab evaluation, gauging the extent of free product, as observation wells for pilot testing, or determination of the direction of groundwater flow.
Direct Push Technology (DPT) is best suited for screening sites with an intermediate water table (up to 25 feet to 30 feet BLS), complicated lithology and/or an estimated large plume. Typically, DPT can be used only to install wells of up to 1.5 inches in diameter, with a pre-packed well screen, due to the limitations in borehole diameter that are available to DPT. For 1-inch ID or greater microwells installed with a direct-push rig, there is no minimum annular space requirement because the microwells must be installed with pre-packed well screens. However, microwells are not well-suited for installation in finer-grained materials such as silts and/or clays.
DPT/Combo rigs using hollow stem augers for monitoring well installation are best suited for screening sites with an intermediate water table (up to 25 feet to 30 feet BLS), complicated lithology and/or an estimated large plume. The requirements for monitoring well installation are the same as for conventional (auger) rigs and sonic drilling. DPT/Combo rigs are limited to approximately 25 feet to 30 feet depth due to the lower power available to the smaller rigs, but have the advantage of lower boom height and a smaller footprint.
Auger drilling and mud rotary is best suited for screening sites with a deep water table (greater than 30 feet BLS) where rock is not to be encountered, due to the additional power available to the larger rig. Mud rotary drilling is typically used only to advance the borehole for a deep monitoring well when there is a surface casing in place.
Sonic drilling is best suited for screening sites with a deep water table (greater than 30 feet BLS) or where rock or very tight/stiff lithology or voids are expected to be encountered. Sonic drilling also can be used to install deep monitoring wells without a permanent surface casing, using larger-diameter sonic casing as a temporary surface casing during well installation. Using the temporary override casing will generally save time since all drilling for the well can be performed in one day, rather than having to let the surface casing and grout sit for 24 hours before drilling out for the monitoring well.
Monitoring Well Spacing
Generally, monitoring well installation should be performed following the initial soil sampling, and one monitoring well should be installed per source area, at the location with the highest petroleum hydrocarbon exceedances based on the laboratory analytical data. If no soil impacts are reported, a confirmatory monitoring well location should be selected based on data collected during the soil sampling (OVA, odor, staining, etc.) or based on the most likely area of potential discharge.
As a general rule, additional monitoring wells that are installed outside of the source areas should be spaced apart by 30 to 50 feet. The larger spacing should be employed farther away from the source areas for sites that have very high dissolved concentrations and for sites that have very deep water tables. The spacing of wells may be decreased or increased depending on access issues, delineating the extent of free product, and the dissolved contaminant levels that are detected. If remediation is anticipated, and after consultation with the team professional engineer, monitoring wells may be spaced at tighter intervals to aid in remediation design.
For any assessment investigation where contamination is detected, there needs to be a minimum of three water-table monitoring wells or piezometers installed in order to determine the direction of groundwater flow. The wells should not be installed in a line, but should be installed in a triangular manner so that the direction of groundwater flow can be determined with greater certainty.
In order to horizontally delineate the groundwater plume, step-out wells should be placed north, south, east and west of the impacted well, so that monitoring wells that report hydrocarbon concentrations less than the CTLs surround the dissolved hydrocarbon plume, at approximately 30-foot spacing (depending on site conditions/obstructions).
As an assessment progresses, the need for and placement of additional monitoring wells must be evaluated. The following are general guidelines to be followed:
- If the dissolved contamination in the groundwater exceeds the natural attenuation default concentrations for source wells, then the plume should be “chased’ horizontally and vertically. Exceptions to this are:
- Physical barriers in the way (e.g., buildings and very wide roads).
- The existence of a confining clay layer greater than 5 to 10’ thick vertically that is laterally continuous across the area of the plume. The existence of the confining clay layer must be agreed upon by the consultant’s professional geologist of record and the PRP’s professional geologist of record. (NOTE: For the purposes of this guidance document, the terms confining, semi-confining and retarding are subjective. Geotechnical testing is rarely completed on the soils before monitoring well installation, so the lithology description is generally based on a field interpretation.)
- The resampling of the vertical extent well indicates that the dissolved contamination detected in the first groundwater sampling event in excess of the natural attenuation criteria does not represent the actual dissolved concentrations in the formation. Frequently, the first groundwater sampling event that is conducted for a vertical extent well may erroneously indicate that the results are in excess of the natural attenuation criteria. This “false positive” occurs as the result of the “dragging down” of soil or groundwater contamination from the shallow zone during the installation of the single or double-cased vertical extent well. Before any additional vertical extent wells are installed to define the base or lateral extent of the plume in the deep zone, the vertical extent well should be evaluated for resampling to confirm the first groundwater analytical results.
- If groundwater contamination exceeds the groundwater SCTLs but is less than the natural attenuation default source concentrations, an evaluation of whether to “chase” the plume should be made on a case-by-case basis as outlined below:
- Temporary groundwater screening samples obtained using direct-push rigs are generally from very short-screened intervals located at the water table. Groundwater samples obtained from permanent monitoring wells that have a longer screened interval and are installed at the same locations of the direct-push groundwater screening locations often display a decrease or non-detect contaminant levels.
- Where groundwater cleanup target levels are only slightly exceeded in monitoring wells, it may be possible to use isoconcentration contour lines to estimate the extent of the plume on the source property, and avoid installing additional permanent monitoring wells to locate the exact spot where the dissolved contamination is at or below the cleanup target levels. Isoconcentration contour maps must be submitted with multiple contour lines, which demonstrate the concentration gradient across the plume. Logarithmic contour lines (e.g., 10,000 ug/L, 1,000 ug/L, 100 ug/L, 10 ug/L and 1 ug/L) are preferred to show plume characteristics for sites with high concentrations.
- If potable well(s) or other receptors are reasonably close, especially in the downgradient direction, additional monitoring well installations to better define the plume are warranted.
- If the site will undergo natural attenuation monitoring and there are no offsite access issues, there must be a monitoring well demonstrating a clean downgradient point of compliance.
If petroleum hydrocarbon concentrations exceeding CTLs exist at the property boundary, then off-site access should be requested to install off-site monitoring wells to fully delineate the plume. Off-Site Noticing documents are required only if laboratory-verified petroleum impacts are identified in an off-site property. However, TPOC noticing is required if the off-site wells are clean, but required for continuous monitoring. See Notices SOP section for more information.
During LSA investigations, the purpose of assessment is to determine the presence or absence of petroleum impacts and the approximate size of the plume. Therefore, a larger spacing (approximately 50 feet) can be used when stepping out from the source areas. At smaller sites, it may be appropriate to place step-out monitoring wells at the site boundaries in order to determine if groundwater impacts have migrated beyond the site boundaries.
Deep Monitoring Wells
Vertical extent wells should be installed next to or slightly downgradient (within 5 feet) of the most contaminated source wells. For sites that have multiple source areas, a vertical extent well should be installed at each source area where the dissolved concentrations exceed the natural attenuation default source concentrations that are specified in Table V of Chapter 62-777, F.A.C., where public or private supply wells are located in close proximity to the plume of supply well impacts have been documented, or in areas with a known or suspected high vertical (downward) hydraulic gradient or where there is reason to believe the plume is being pulled downward.
If impacts exceeding NADCs (or GCTLs if team PG is in agreement) are reported at the deep well, then step-out deep wells (set at the depth of the impacted monitoring well) should be installed for horizontal delineation, and a deeper interval monitoring well should be installed next to or slightly downgradient (within 5 feet) of the impacted well to vertically delineate the groundwater impacts.
If a confining (retarding) interval is identified during the drilling activities, the top of the filter pack for the vertical extent well screen should be at least 2 feet below the confining interval. If an OVA/FID is utilized for screening purposes, the OVA data should be collected from above and below the water table. A sharp decrease in OVA readings can be used as an indicator in determining the depth of the plume and the placement of the screened interval. If the lithological data indicate that a retarding unit is not present and the OVA data cannot be used to approximate the base of the plume, then the top of the screen for the vertical extent well should be installed between 10 to 20 feet below the bottom of the screens of the water-table wells.
Monitoring Well Construction
For water-table (“shallow”) monitoring wells, 10 to 15 feet of screen should be used to bracket the water table during the seasonal fluctuations of the water table. Water level elevation should be estimated based on soil sampling and lithology, and temporary monitoring wells/piezometers if possible, and historical information if available. The top of casing should be no less than 2 feet below land surface to allow enough space for a surface seal and the manhole and well pad.
The maximum screen length for a vertical extent well should be 5 feet (or more if the screened portion of the aquifer is slow to recharge). Due to the short screened interval, proper placement of the screen within a permeable interval is preferable. If it is suspected that the vertical extent well will not yield a sufficient water sample due to the confining or retarding nature of the soils, then consideration should be given to collecting a soil sample for lab analyses at the base of the vertical extent well. This result will provide additional information along with the OVA data as to the vertical extent of the plume. The surface casing should be installed within a confining layer, if observed, in the upper 2 feet of the confining layer, or at least 10 feet to 20 feet below the bottom of the shallow (or intermediate) monitoring wells. The top of the filter pack for the vertical extent well screen should be separated from the surface casing by a minimum of 3 feet (our standard is typically 5 feet). This should help prevent any cross contamination resulting from the installation of the surface casing.
The diameter of the surface casing should allow for the proper placement of the well casing and the 2-inch minimum annular space for the filter pack. Triple casing may be considered at sites with very high contamination levels (free product), significantly contaminated intermediate zones, and/or large vertical hydraulic gradients. On a site-by-site basis, an evaluation should be made as to the need for additional casing to segregate lithologic/hydrologic units by separate casings. If additional vertical extent wells are needed to determine the lateral extent of contamination observed in the initial vertical extent well, a review of the shallow aquifer contamination levels should be performed to determine if a surface casing is needed for any of the additional wells.
Groundwater Sampling
Monitoring wells should be sampled at least 24 hours after monitoring well installation and well development has been completed. In general, only newly-installed monitoring wells should be sampled during each sampling event, unless there are existing monitoring wells that show fluctuations in petroleum hydrocarbon impacts or are specifically requested by the ATC or PRP personnel, with PRP approval.
If the site assessment period lasts more than 270 days from the initial assessment field work, then the final groundwater sampling event should include sufficient source and perimeter wells to show the extent of the dissolved hydrocarbon plume in one snapshot.
Laboratory Samples
During the initial groundwater sampling event, one sample should be taken from each potential source area for GAG/KAG or Used Oil Group, depending on the contents of the storage tanks, and the remaining groundwater samples analyzed for BTEX/MTBE, PAHs and TRPH by the appropriate analytical methods. The results of the initial sampling event should be used to determine what laboratory analytical methods are required for subsequent sampling events.
Site Assessment Report Review and Approval
The Agency Term Contractor must submit documentation that the work required by the Purchase Order has been successfully completed. There are two types of deliverables: interim deliverables and final deliverables. To facilitate interim invoicing points, an interim deliverable must be established for each individual event and may include well logs, analytical reports, delivery receipts, etc., as invoicing support, or a technical report such as an Interim Assessment Report or a Remedial Action Interim Report. Typically, the final deliverable of a site assessment Purchase Order is a technical report such as a Site Assessment Report (SAR), Supplemental Site Assessment Report (SSAR) or Site Assessment Report Addendum (SARA).
Interim Reports
An Interim Assessment Report is required when site assessment work in the initial stages of a purchase order will be used to determine the technical approach for subsequent sampling event and where there is a need for evaluation and discussion of activities and data. The Remedial Action Interim Report is approved in several different post-SAR situations where there is a need for evaluation and discussion of activities and data pertaining to interim events that occur after SAR approval but are not addressed in other specific RAP or RA reports, including but not limited to well installation (monitoring or remediation), soil screening and verification sampling, and associated updates of maps and tables. The interim report should include tables and figures documenting the new assessment data and recommendations for additional assessment work, if required. If all that is required is documentation of work performed, then the interim deliverable should consist of a letter report documenting the activities and invoicing support documents.
Final Reports
Assessment reports that are intended as a final deliverable before Active Remediation or Natural Attenuation Monitoring (NAM) should be a comprehensive and final site assessment deliverable documenting all site assessment activities completed up to the point of site assessment phase approval and should include recommendations for the next phase of work, signed and sealed by a registered professional geologist or qualified registered professional engineer.
Deliverable Reviews
If the Purchase Order task includes both field work and a technical report, then deliverable reviews for completeness should be completed within ten (10) days of receipt of the deliverable. This determination of “complete” does not necessarily mean that the deliverable will not need any further revision; it means only that all required information to support work completed for invoicing appears to be present. The technical report deliverable should not be approved until all of the required information and documentation is included and is correct. This means that all tables and maps are correct and up to date, that all required backup information (e.g., soil boring logs, well installation logs, laboratory analytical sheets, chains of custody, sampling logs) is included and complete, that the document text accurately presents and describes the results, and that conclusions and recommendations are included. If the document is deficient in an area that should have been addressed, then the Agency Term Contractor must correct the deficiency at no additional charge. Each Site Manager must work with their Section Geologist on all Site Assessment issues.
After each interim or final deliverable has been reviewed, the Site Manager must send written notice of deliverable acceptance (for completeness – not full review) or approval, as applicable, to the Contractor within the required time frames. See the Report Turnaround Times Table for site manager time frames for review of technical report deliverables. If any of the work was unacceptable, then the letter also must specify what corrections or additions the Contractor must make, or specify what reductions will be made to the Purchase Order.
Some of the technical documents submitted in the Petroleum Restoration Program are required to be reviewed, signed and sealed by a licensed professional and may also require a licensed professional for review and approval by DEP. See Division of Waste Management Policy on Professional Certification of Technical Documents for P.E./P.G. review requirements.
Required Documents
The following documents should be included as part of the invoicing packages, and as an appendix to the assessment report associated with the field work being performed. Standard formats are available from the links provided.
- Site Access Agreements (if applicable)
- Applicable Tables and Figures
- Field Notes
- Soil Boring Log
- Well Construction and Development Log
- Groundwater Sampling Log
- Laboratory Analytical Reports with:
- Chain of Custody Record (PDF)
- Instructions (PDF)
- Any other required documentation noted in the Scope of Work
- Receptor Survey and Potable Well Information (final site assessment report only)
- Site Assessment Summary Worksheet (final site assessment report only)
Return to: PRP Site Manager Standard Operating Procedures (SOP) webpage.
Return to: SOP Site Manager Guide webpage.
Interested in subscribing to DEP newsletters or receiving DEP updates through email?
Sign UpAbout DEP
The Florida Department of Environmental Protection is the state’s lead agency for environmental management and stewardship – protecting our air, water and land. The vision of the Florida Department of Environmental Protection is to create strong community partnerships, safeguard Florida’s natural resources and enhance its ecosystems.
Learn MoreContact
3900 Commonwealth BoulevardTallahassee, Florida 32399-3000 Public.Services@FloridaDEP.gov 850-245-2118
